We try to keep the sourcing process as smooth and efficient as possible. You as a customer can be involved every step of the way or keep a hands off approach. The quality of work we do is never compromised
What do you need to do?
- Share your requirements and artwork: This includes as many details as possible regarding specifications, packaging, and quantities. You can also share pictures of products you’d like to customise or private label. We’ll do the rest for you.
- We share quotes received from different suppliers with potential issues and risks regarding the suppliers.
- We send samples and a detailed report about the production timeline.
- You accept the quote after approving samples; Products are shipped to you and you receive goods timely.
What does our in-house sourcing process look like?
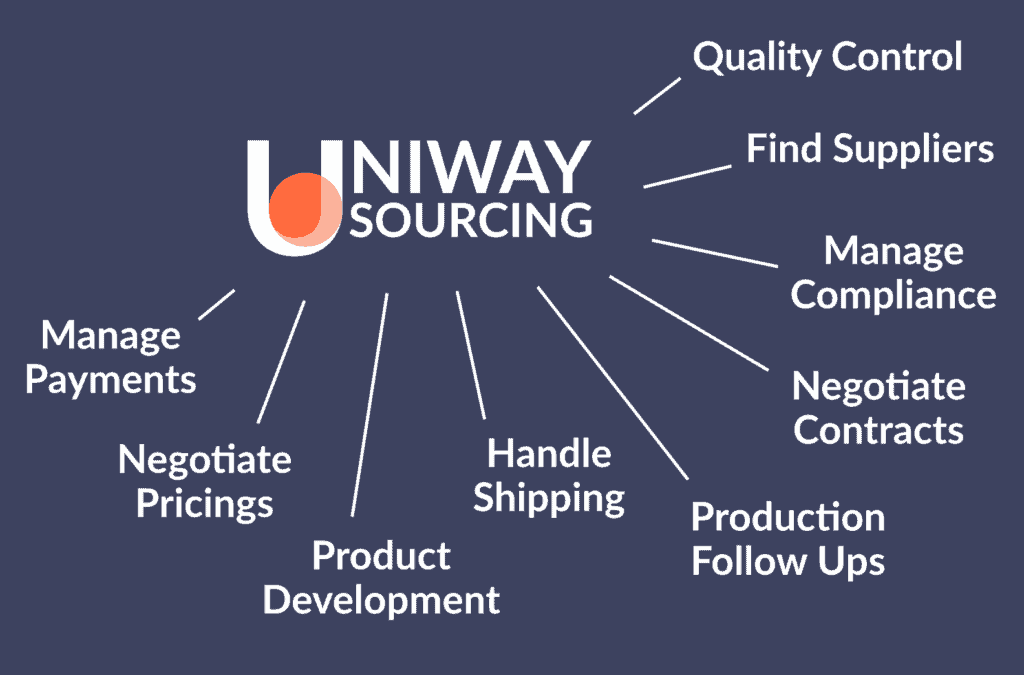
- Requirements: We study your requirements in depth to develop a complete understanding of your current scenario and needs. We discuss potential issues, usage of your products and scenarios based on your sales channel
- Artwork: If you have sent us artwork or drawings, our production analysts study them to find potential issues and suggest modifications. This is done to improve the quality of the end product while at the same time reducing costs. In cases where artwork has not been developed, we help guide you in the right direction.
- Supplier Identification: We create an in-depth product specification sheet which is sent to suppliers we think would be suitable. In many cases, we already have shortlisted suppliers in our database which are capable of producing your products. When identifying suppliers, we also take into account raw material costs and the work required. This gives us an idea as to what the best choice would be based on quality, price and performance.
- We send you quotes: Our quotes include a detailed analysis of each supplier, we identify each supplier’s limitations and costs. We also recommend the best choice based on the best price to quality ratio.
- Supplier Audit: This step is only carried out when working with a new supplier. Our auditor goes to the factory and audits its systems. The auditor also notes the number of workers, machinery and capabilities, current production, factory environment, SA8000 compliance (social audit), management, quality control processes and recent exports.
- Sampling: We discuss with the supplier the lead time required for sample production. We also ensure they understand all your requirements. After a sample is handed over to us, we approve or reject it based on our judgment. If a sample is approved by us we send it to you for review. We expect the supplier to have the same quality of products during mass production. Approving only the highest quality of samples is of utmost importance.
- Production: We conduct a pre-production inspection at the factory to ensure the appropriate raw materials will be used in mass production. After production has started we send our quality inspectors at mid-production as well as a pre-shipment inspection to ensure the quality is consistent. A pre-shipment inspection also includes checks for packaging and shipping marks.
- Shipping/Delivery: We will arrange for the cargo to be picked up by a freight forwarder. We ensure all documentation is in line, as we will be handling the customs process for your products. We keep you updated regarding the delivery dates for your order.
- Goods are received by you: The shipment is delivered to your choice of location; we ensure you are happy with your order.